Personnel qualification as an indispensable part of modern technology transfer
Personnel qualification as an indispensable part of modern technology transfer
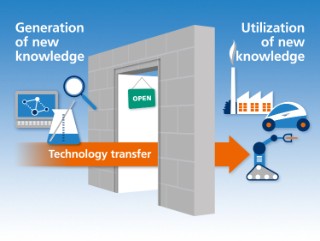
Technology transfer as a ‘door opener’ between research and application-related utilization
New developments thrive on research and development, i.e. on the generation of new knowledge. New knowledge is not an end in itself. New knowledge must find its way into application in order to be economically viable. To do this, it must be transferred from research and development to the manufacturing companies in industry and handicrafts. With its further training offers, the Fraunhofer IFAM is working to simplify this process. Successful and long-term technology transfer is only possible through the qualification of company personnel and the structuring of the organization of company production processes.
more info